Six Steps to Appliance Product Development Cycle
Iron’s quality management system incorporates a formal product realization process for taking a new product from conception to full production and post-sales support. There are six major stages to Iron’s Appliance Product Development Process:
Read More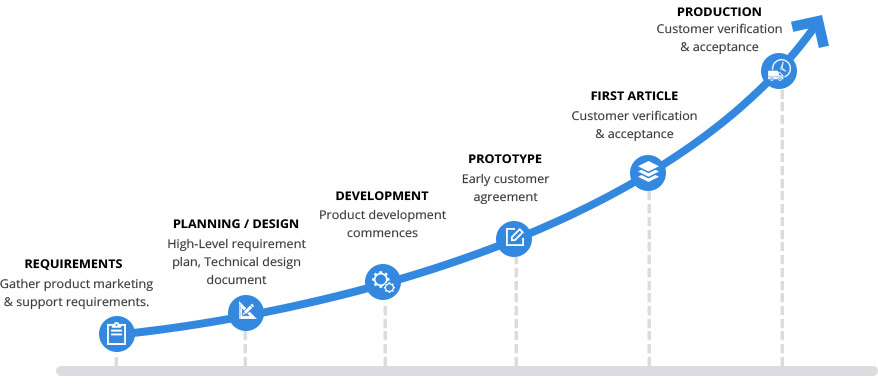
- Requirement Gathering: Our Product Management and engineering staff works with the customer to gain a complete understanding of the application software and its environment, and to help define hardware requirements. We then configure a system which forms the basis of a preliminary high-level requirements document (HLR) created by our Engineering Department. A written proposal is submitted which outlines the planned schedule, deliverables, costs, warranty, support, branding, and all other relevant issues. Upon customer acceptance we move into the planning/design phase.
- Planning/Design: The HLR is finalized with details that serve as the preliminary Technical Design Document and as the Customer Requirements Checklist against which verification and validation are performed.
- Development: Product development work commences. An early prototype is produced which has the same internal components as indicated in the HLR. Some of the other product elements may be missing or different however, the goal is to get early concurrence on the fundamental product under development.
- Prototype: Prototypes are thoroughly tested for form-fit and operating system compatibility. The prototype is subjected to extensive thermal testing, ensuring adequate cooling for all internal components. We also use the customer’s functional test scripts to run “close-to-real” testing. During the development stage we create detailed work instructions for the final production units and design customer packaging materials. The prototype appliance must be approved by the customer, before any further development is performed.
- First Article: When the prototype is accepted, Product Management and Engineering completes development and delivers the first article for final verification and acceptance. The appliance is assembled and tested using the work instructions written during the development phase. Thorough quality checks are executed and quality control documents are finalized.
- First Customer Ship (1st Build) & Production: Production commences when the First Article is accepted by the customer. Product Management and Engineering will prepare and transfer to their production counterparts all material and information necessary for volume production in stages. The production staff will receive training on assembly, test, and burn-in procedures. At this point, the Program Management team will assume responsibility for the project and manage day-to-day operations as well as become the "point of contact" for customer communications.